Since 2010, SIEMAG TECBERG has continuously optimised and expanded its product assembly and system testing capacities. This means that the SIEMAG TECBERG group make use of a high-performance, high-tech workflow to realise customer-specific projects in medium to heavy machinery and plant engineering. Everything is designed to implement the best solutions under the best conditions and with the highest efficiency. As a supplier of complex systems, it is especially important to coordinate the mechanics, hydraulics, and drive and automation technology in a system-integrated manner.
TECBERG park System Test Areas
- Product Assembly 1
Since 2010 SIEMAG TECBERG has utilised this 2,600m² area, fitted with cranes capable of lifting assemblies of up to 40 t, for product and component assembly of light to medium-heavy parts. Brake elements and their corresponding hydraulic power systems, including control and regulation systems, are also assembled and tested here. - Product Assembly 2
This is where the project related product assembly of heavy machinery and plant takes place. With a floor space of 2,500 m², this area has been designed for heavy products and components weighing up to 200 t in total. Within this area there is a large 12 x 18 m test bay with own power supplies and automation to enable mechanical and hydraulic control testing and commissioning under real conditions. - Product Assembly 3
Designed for the assembly of medium-heavy products and components, with a total weight of up to 40 t, this 1,800 m² area is used for project related assemblies. Power supplies and automation is also available here in the 5 x 10 m test area enabling mechanical, hydraulic and control testing and commissioning to take place under real conditions.

System integration of mechanics, hydraulics, automation and drive technology
As part of the testing on the test benches in the assembly plant, a system test can be performed that includes the pre-optimisation of the entire drivetrain. Once all of the individual components have been parameterised the system is tested in various operating conditions and with different acceleration and deceleration phases.
Testing and optimisation is also carried out at a standstill whilst applying torque. This comprehensive approach provides the foundation for reliable plant operation after assembly on site. Furthermore, by carrying out the optimisation of the individual components prior to delivery SIEMAG TECBERG is able to offer a significantly faster and more straightforward commissioning and start-up phase of the system once on site. These benefits subsequently translate into increased uptime once the system is in operation on site due to SIEMAG TECBERG’s comprehensive factory testing and commissioning programs.
Mechanics / Hydraulics
A component level inspection checks the dimensional accuracy of function relevant system dimensions, such as shaft/rope carrier, shaft/motor, shaft/bearing connections. When the complete hoisting machine is commissioned at the factory, the drive is rotatated and the rope carrier and brake are made ready for operation.
Optimisation and testing of the following ensures a high level of quality is attained:
- Measurement of the air gaps between the brake elements and the brake disc
- Concentricity measurements of the brake discs on the rope carrier
- Reduction of geometric unbalance
- Avoidance of eccentricity
- Verification of axial and radial forces
- Verification of spindle and shaft torsion
- Reduction of excessive dynamic vibrations and noise development
- Checking of operating temperatures in slide and roller bearings
- Determination of the operating behaviour (temperature, pressure, etc.) of units
- Verification of the operational behaviour of gear units and clutches in use
- Factory adjustment of the complete brake system, incl. analysis of brake curves
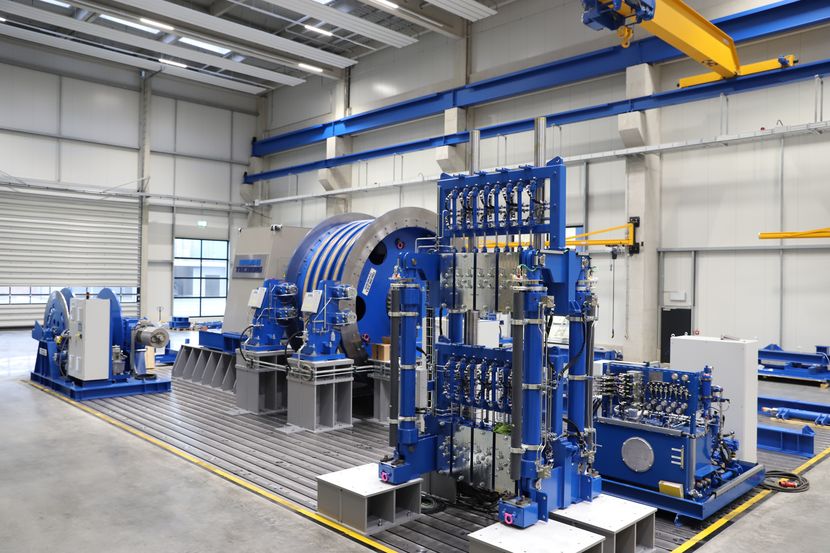
Automation and drive technology
An interface verification takes place between the mechanical, hydraulic, automation, converter systems and auxiliary controls:
- The interaction between automation and the braking system on the "rotating system" is checked
- The controllers are parameterised
A process simulation is carried out to test control sequences and correct operation of the various operating modes.
Optimisation of the entire electric drive concept with regard to the total moment of inertia:
- Analysis of motor characteristics, e.g. insulation and resistance measurements, no-load characteristics at nominal voltage
- Heating under load
- Testing and optimisation of the motor and control behaviour at standstill torque (speed n = 0)
- Testing of the behaviour at different starting torques, load jumps and load cycles
Improved customer benefit thanks to System Factory Acceptance Test (FAT)
- Significantly increased functional safety for the overall system resulting from the integrated functional tests as described above
- System FAT offers customers greater planning certainty for the entire mine production plan during the commissioning on site
- Reduced assembly and commissioning time on site thanks to factory setup and factory commissioning (parameterisation)
- Variant simulation for the optimisation of assembly and commissioning on-site as support for customer planning
- Documentation of system parameters is available earlier to support approvals and certifications
- Improved process descriptions for the erection of the plant through modularisation of assembly and commissioning processes
